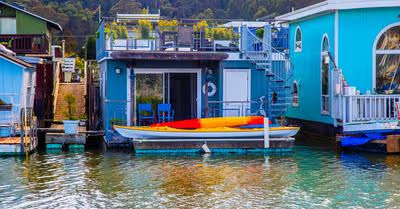
Houseboat manufacturing is a complex process with multiple steps. Building a houseboat takes skilled craftspeople and marine designers.
Houseboats begin as a set of plans and patterns, which are scaled up into a mold. The hull and superstructure are molded with fiberglass and joined together. Then, workers outfit the vessel with windows, engines, appliances, wiring, and interior fittings.
In this article, we’ll go over all of the major steps that go into building a houseboat. We’ll cover the materials used to build houseboats and focus primarily on fiberglass due to its widespread use. Additionally, we’ll cover some other common houseboat materials and construction methods, such as plywood, steel, and aluminum.
We sourced the information used in this article from houseboat makers. We carefully researched the steps involved in houseboat manufacturing and studied the process from start to finish.
What are Houseboats Made Of?
Most houseboats are made of fiberglass. Fiberglass, when combined with resin, becomes hard and waterproof. The brilliant thing about fiberglass is that it can be molded to any shape, and when it dries, it is rigid enough to form structural walls and completely waterproof.
American houseboats are sometimes made of aluminum or steel, which is stronger but costlier than fiberglass. Some houseboats are built from a combination material and placed on pontoons, which are prefabricated and made from stainless steel.
The vast majority of fiberglass houseboats also incorporate a large amount of wood, which is used as a core for the fiberglass or as additional structural support. Some houseboats, especially premium models, use steel or aluminum framing in place of wood.
There was a brief period of time during the 20th century when houseboats were sometimes built using an experimental boat building material called ferro-cement, but this material has largely disappeared from the houseboat building world.
Plywood is used for many home-built houseboats and small-scale production operations. Plywood, which is almost always glassed-over with fiberglass and resin, is a good amateur boat building material but costlier on a large scale than all-fiberglass models.
How Fiberglass Houseboats are Built
Now, we’ll go over the basic steps required to build a houseboat out of fiberglass. This is how most production houseboats are manufactured. We chose to focus on fiberglass construction because it’s the most common and one of the simplest ways houseboats are built.
Step 1: Design and Planning
Design and planning are essential to the early stages of building a houseboat. This is the blueprinting phase of construction and results in detailed build plans that cover every aspect of construction.
Marine architects and engineers start with a basic idea of what they want to design. They may draw some rough sketches and a floor plan and then begin the more complicated aspects of the design process.
Hull lines are drawn, which are a scaled-down but accurate reference for the actual boat. Additionally, the superstructure is drawn to scale and arranged. Once the basic hull shape is complete, engineers go to work designing the systems that are necessary to make the houseboat function.
This is the stage of development where engineers figure out where to put the engine, the length of the shaft, the location of hydraulic lines, electrical schematics, and more. This should be completed before any construction begins.
The interior is also arranged, and adjustments are made wherever necessary to accommodate essential systems and machinery. Designers must work carefully with engineers to ensure that every essential part has a place, every wire has a conduit, and no interior furnishings interfere.
Step 2: Houseboat Patterns and Molds
Most production fiberglass boats are made using a set of pre-built reusable molds. This greatly increases the speed and cost-effectiveness of production and also improves the accuracy of the building process.
Molds are constructed based on the specifications indicated in the plans.
The mold is constructed from numerous materials—often plywood and metal. It’s lined to prevent fiberglass from sticking, and the inside is completely smooth and the exact opposite of the boat shape.
The wood used to build the mold is cut by a computerized saw, which matches the dimensions exactly to plans, which must be precise if the casting is to be correct. The mold is then coated in fiberglass and painted with a highly durable coating.
Multiple molds are involved in the production of fiberglass houseboats. The most important and complex mold is usually for the hull. The superstructure is molded separately, often in multiple parts.
Step 3: Casting the Hull and Structure
Fiberglass houseboat hulls and superstructures are made from a combination of fiberglass and epoxy resin, which hardens the strong and fireproof material into an impermeable solid. These materials are mixed to exact specifications in a machine and sprayed onto the mold by a skilled technician.
The mold can be rotated in either direction to allow the technician to reach all the angles without stepping on wet fiberglass. The beautiful thing about fiberglass is that it can be applied over dried material at any time, so the process is completed in several parts.
The technician will do the majority of the work with a spray gun, but other workers will apply additional material and roll it into key structural areas for additional support. Most of this work occurs in the sharp corners of the hull.
The superstructure is cast the same way. The workers spray fiberglass onto the mold, and then workers go over key areas by hand to ensure their structural integrity.
Eventually, the hull and superstructure molding will be complete, and the units left to dry. Once cured, which can take several days, the finished hull and superstructure are lifted out of the molds, and the excess is trimmed away. An additional layer will be added to the fiberglass as a laminate to keep moisture out and to add an additional level of strength.
Step 4: Finishing the Hull and Superstructure
The hull and superstructure are molded without any cuts or holes for machinery and fittings. Once cured and removed from the mold, workers use the plans and patterns to identify the location of key parts and make cuts.
Workers cut out doorways, window openings, holes for wiring and pipes, and ventilation holes wherever necessary. Then, wooden supports are added in key locations like window frames and under the deck, then encapsulated in fiberglass for strength and moisture resistance.
Step 5: Joining the Pieces
At this point, the separately-cast pieces will be joined together. Sometimes, the installation of engines and other heavy parts occurs before the superstructure is joined to the hull.
The pieces are bolted, glassed, or joined together with screws. The gaps between the hull and the superstructure are sealed and structurally sound thanks to additional fiberglass material.
Step 6: Outfitting
During the outfitting phase of construction, all other parts and fittings are installed and readied. Things like cupboards, carpet, furniture, and paint are applied at this stage. Outfitting is one of the longest of the production stages and also one of the most involved.
This process requires the skills of many different craftsmen, including cabinetmakers, electricians, carpenters, and sometimes welders and metal workers. Wiring, switches, pipes, utilities, and mechanical systems are installed and inspected.
Insulation also happens during this time, and surfaces like non-skid decks and flooring are installed. Appliances, sinks, and toilets are carefully lifted onto the vessel and secured, with all wiring and connections made. Sometimes mattresses and fixtures are also added.
The majority of the parts installed at this time are pre-manufactured. Hatches, doors, lights, and electronics are made by different companies and integrated into the vessel based on the designer’s specifications.
Many different options for layout are available at this time, and the builders will follow the select floor plan. Custom houseboats are usually built from stock plans up to this point when designers and the future owner get a say in the final design.
The outfitting stage is when the boat will begin to look and feel like a houseboat. It’s also the most important stage for fit and finish, as the materials used inside and around the boat can vary in quality based on the trim level and final cost.
Material selection is often up to the customer. They can choose hardwoods or veneer for cabinets, floor or carpet, and the type of countertops used throughout the vessel. Additional options, such as central heating and air conditioning, are assembled and installed at this time.
Step 7: Final Preparation
The final stage of production adds the finishing touches to the vessel, along with the final bits and pieces. Sometimes trim is installed at this stage. Other items, such as ladders, light bulbs, and cushions for seats, are installed or placed inside the boat.
Safety equipment, such as smoke detectors, carbon monoxide detectors, and fire extinguishers, are often added at this time as well. A bit of paint is often applied here and there, and the vessel’s decals are laid carefully on the hull.
Final cleaning and inspection occur before the boat is shipped to its final destination or dealership. Workers dust off surfaces, vacuum and sweep up any remaining sawdust, and pick up any debris remaining from the outfitting stage.
Parts may be polished, and protective plastic gets removed from surfaces. Sometimes, the dealership receives the boat with all of the protective plastic and labels still on the parts.
Once the paperwork is complete, and a final inspection is done, some of the systems (like the engine, generator, and electrical systems) may be tested. Batteries may be added, but some companies leave parts of this stage up to the dealership or owner.