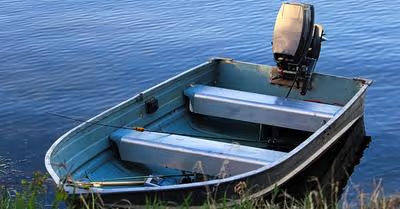
Key Takeaways
- The three common causes of pin holes in aluminum boats are galvanic corrosion, stray current corrosion, or mechanical damage.
- You can fix the pin holes by welding them or using an epoxy primer to seal the area.
- Regular boat maintenance is the best way to prevent pinholes in your boat.
When I first saw pinholes in my aluminum boat, I realized how crucial it is to address this issue promptly. But what causes it, and how do you fix it?
Pin holes in an aluminum boat can appear because of galvanic corrosion, stray current corrosion, or mechanical damage. You can either weld the holes or use an epoxy primer to patch up the holes. Pin holes can also occur if your aluminum boat is wrongly exposed to salt water.
Aluminum boats are popular for being lightweight and low maintenance. However, they can be susceptible to pinhole formation if the right alloy isn't used. This guide is my step-by-step guide for dealing with this issue based on past experiences.
Pin Holes In Aluminum Boat: Causes
Aluminum boats are popular among boaters for their durability, strength, and resistance to corrosion. However, even the strongest aluminum boats can develop pinholes over time, leading to leaks and other serious issues.
Galvanic Corrosion
One of the most common causes of pinholes in aluminum boats is galvanic corrosion. I've noticed that this occurs when dissimilar metals come into contact with each other in the presence of an electrolyte like saltwater.
Aluminum, less noble than other metals, serves as an anode and corrodes faster, leading to pinholes. To mitigate this issue, I always recommend using sacrificial zinc anodes on your boat that will corrode instead of aluminum.
Stray Current Corrosion
Another cause of pinhole formation I've seen is stray current corrosion. In this case, a small electrical current discharges onto the aluminum hull, causing it to corrode. Double-check the ground wire too.
The most common sources of stray current in boats include electrical wiring issues and faulty equipment. I believe regular inspection of onboard electronics can help prevent stray current corrosion - just make sure to check for proper grounding and tight connections.
Mechanical Damage
Lastly, mechanical damage can contribute to pinholes in aluminum boats. Over time, rocks, debris, and even barnacle growth may lead to abrasion or damage to the boat's surface.
I suggest regularly inspecting the boat for any signs of damage and addressing them immediately to avoid further deterioration. A careful cleaning and routine maintenance should help protect the boat's hull from mechanical wear and tear.
How Can You Repair Pin Holes in Aluminum Boats?
Now that we know what causes these pesky pin holes, let’s try to fix them. Here are a few repair methods that worked for me.
Welding
One method I've used to repair pinholes in aluminum boats is welding. It's a process where a filler material, usually aluminum wire or rod, is melted along with the boat's metal, creating a solid bond between them.
This permanently seals the pinholes and prevents water from seeping through. Before welding, clean and sand the area to remove any dirt, debris, or corrosion for the welding process to be effective.
If you only have small pin holes, welding is probably not necessary. Instead, you can opt for a faster solution that won’t permanently change the finish of the metal surface.
Epoxy Repair
Another approach I've had success with is using an epoxy repair kit specifically designed for aluminum boats. The West System aluminum boat repair kit typically includes a 2-part epoxy adhesive that you mix, apply to the pinholes, and allow to cure.
Once cured, the epoxy forms a strong, waterproof bond that can help prevent further pinholes from forming. We recommend using JB Weld to repair the pin holes quickly. JB Weld is also extremely cheap.
Marine-grade paint or Marine Tex will also work. These solutions work exceptionally well for saltwater aluminum boats with small holes along the hull.
To use an epoxy repair kit, follow these steps:
- Wash: Rinse off any dirt from the aluminum surface.
- Abrade: Use sandpaper or a sanding block to remove any corrosion around the pinholes
- Buff: Use a rotating buffer, wire brush, wire wheel, or fine steel wool to buff the sanded area and make it smooth.
- Apply epoxy: Mix the epoxy adhesive according to the kit's instructions and apply it to the pinholes, ensuring full coverage.
- Cure: Allow the epoxy to cure for the recommended time on the packaging.
- Polish and protect: Once the epoxy is fully cured, polish the area and apply a protective coating to prevent further corrosion.
Remember, repairing pinholes in your aluminum boat can help extend its life and maintain its functionality. Choosing between welding and epoxy repair will depend on your skill and comfort level, as well as the availability of tools and materials.
Identifying & Detecting Pin Holes In An Aluminum Boat
Identifying and detecting pinholes in an aluminum boat is essential to prevent serious damage from occurring. Here are some tips for doing so.
Visual Inspection
During my regular boat maintenance, I always check for pinholes in the aluminum hull. A thorough visual inspection is one of the easiest ways to spot these pesky little holes.
I normally start by cleaning the boat's surface, removing any dirt or debris, and looking for small, corroded areas. While visually inspecting, I pay close attention to worn areas that might harbor hidden pinholes.
Pressure Testing
Apart from visual inspections, I also conduct pressure tests on my aluminum boat to detect pinholes. This method involves:
- Sealing the boat's interior
- Filling the boat with low-pressure air (around 2-3 psi)
- Spraying soapy water solution on the outside of the hull
- Observing soap bubbles that could indicate air escaping from pinholes
Once I identify areas with bubbles, I mark them for further investigation and possible repair.
Pressure testing might seem like a more complicated method, but it's pretty effective in detecting pin holes that aren't visible to the naked eye.
Just remember not to use too much air pressure, as it could cause damage to the boat's structure.
How To Prevent Aluminum Boat Pin Holes In The Future
Ideally, we never want to deal with aluminum boat pinholes. This is what I would do to try and prevent it from ever happening again.
Proper Maintenance
One key to preventing pinholes in my aluminum boat is proper maintenance. I always make sure to clean the boat thoroughly after each use. Dirt and debris can lead to corrosion, so keeping the hull clean is important.
Regular inspections are also crucial. I can prevent pinhole formation by addressing the issues I notice early on.
Galvanic Isolators and Anodes
Another technique I employ to protect my aluminum boat is using galvanic isolators and anodes. These devices help to minimize the effects of galvanic corrosion caused by various metals in electrical contact with each other when submerged in water.
The isolator is installed on the electrical system, while sacrificial anodes are fixed directly onto the hull. This combination effectively absorbs and redistributes the corrosion, so my boat stays protected.
Stray Current Prevention
Finally, I pay close attention to stray current prevention. Stray currents can be harmful to aluminum boats, causing pinholes and corrosion.
To prevent this, I carefully maintain the electrical system on my boat, checking for any potential issues like faulty wiring or damaged insulation.
Additionally, I make sure to use a shore power cord with a built-in galvanic isolator when connected to on-shore power sources. This helps to block potential stray currents from entering my boat and causing damage.
Can You Patch An Aluminum Boat?
Of course, you can patch an aluminum boat. I've had my fair share of experience fixing pinholes in aluminum boats, and I'll walk you through the process. You can follow different methods, so let's go over a couple that might suit your needs.
First things first, always start by cleaning the whole area. I like to rinse off all the dirt from the aluminum surface to ensure it's spotless before moving on to the repair. If you've got some corrosion around the hole, you can remove it by abrading the surface.
Then, you can use a rotating buffer or fine steel wool to buff the sanded area. One common method to patch pin holes is by using an epoxy primer.
After cleaning and preparing the area, I apply the epoxy to the hole and let it cure. Once it's dry, I sand down the repaired area to ensure it's smooth and neat.
Another option I found was using a product called Flex Seal. It's a liquid product you apply to the surface that can cover holes and cracks. It's also non-toxic, making it quite handy.
If you don't have access to welding tools, you can use an aluminum patch with Sikaflex and rivets to fix the hole. This technique is especially useful if there's no option to TIG weld the area.